|
Shop Tour
 |
page 1 | 2 | 3 | 4 | 5 |
 |
Our 10-foot-long, 170-ton, computerized, nine-axis fabrication press features the latest in automation controls. This machine has nine programmable axis, which allow us to make even the most-complicated formed parts. Once a digital model of the formed part is downloaded, the control virtually programs itself. |
Many Chassisworks products are robot-welded. This dual-station robot-welding cell’s simultaneous part rotation and robot movement provide optimum positioning of the work piece resulting in the finest weld quality possible. |
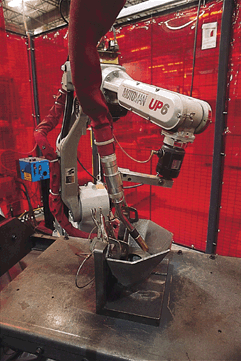 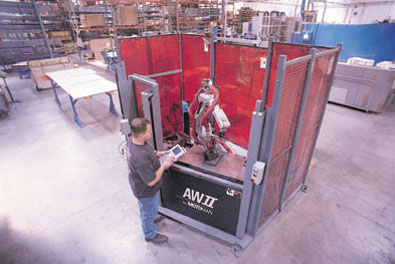 |
We also manufacture parts on a Mazak Pallatech machining center the very first of these huge machines to be delivered in America. Its enormous work envelope enables us to manufacture more parts per cycle. With 12 tables and 120 different tools available, we can machine large numbers of parts with no setup time.
Its 50-horsepower, 15,000-rpm spindle really makes the chips fly! This machine enables us to produce those high-quality, low-cost FAB9 housings.
|
Our investment in technology doesn’t stop here. As many of you have experienced, chromed parts can easily chip and peel. Chassisworks was not at all satisfied with the quality of chrome available. We looked at many alternatives and methods for preventing flaking and peeling. After much investigation, it was determined that polishing a tube prior to manufacture and chroming would result in a premium-quality finish.
Chassisworks did not delay; we went right to work purchasing, installing and utilizing a tube-polishing machine. Now, all parts to be chromed are polished before anything else is done to them. This additional process has helped us bring a more-professional appearance to the finished piece.
|
 |
page 1 | 2 | 3 | 4 | 5 |
 |
|
|